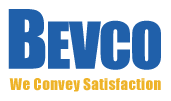
Understanding the Essentials of Conveyor Systems
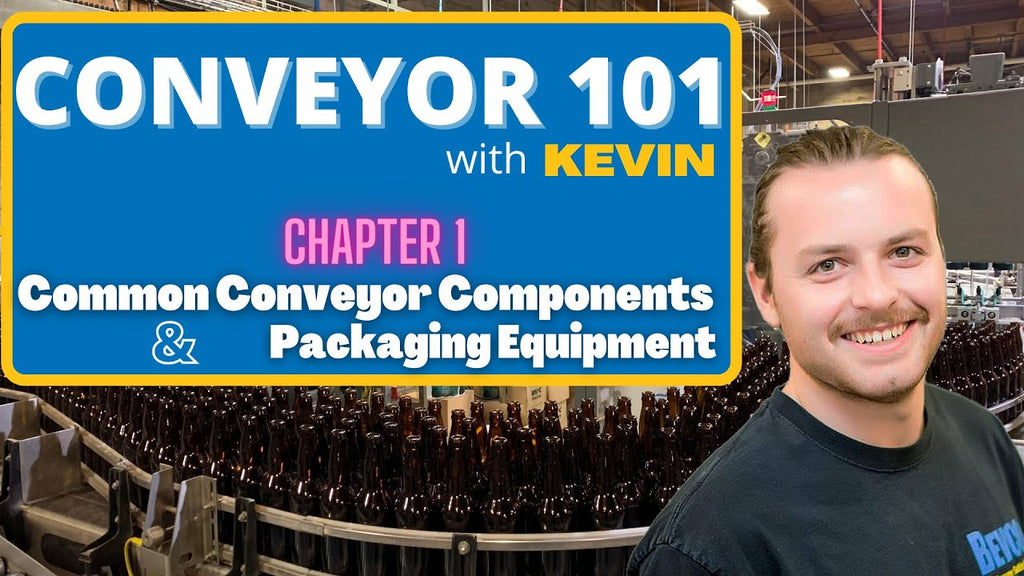
A little while back, we posted one of our most popular videos, a Conveyor 101 crash course that explores the fundamentals of conveyor systems with Kevin, one of our resident EIT’s (Engineer-in-Training). This introductory lesson aims to equip you with a thorough understanding of conveyor system components, their operation, and the technologies that enhance their functionality. We realize that not everyone has the time to watch a 10-minute video (although you should - it's great), so we've distilled the knowledge from this piece of content into a comprehensive blog post. Whether you're pressed for time or prefer reading to watching, this guide serves as an accessible alternative to grasp the basics of conveyor technology.
Introduction to Conveyor Systems
Conveyor systems are the backbone of production lines in almost every industry, from food and beverage to pharmaceutical lines and beyond. At their simplest, a conveyor's purpose is facilitating the efficient transport of containers and products. With the addition of more specialized packaging line equipment, a conveyor serves as the spine of a production line, guiding products through machinery that prepares them for their lives on shelves and in homes. From the frame and chain to the intricacies of the drive shaft and control panels, each element plays a critical role in the seamless operation of the conveyor.
Let's begin by delving into the critical components of conveyor systems, highlighting everything from the structural support and movement mechanisms to the features that ensure cleanliness, efficiency, and precise control.
Key Components of Conveyor Systems
The Conveyor Frame & Chain are the backbone of the system, supporting a chain that carries containers along the conveyor path. This straightforward setup accomplishes the conveyor's primary function: moving products efficiently from one point to another.

Guiderails & Brackets are needed for keeping the products aligned on the conveyor. These adjustable brackets can be shifted to accommodate different container sizes, making it possible to have versatility across various product lines.
Especially in systems where lubrication is used, Drain Pans are strategically placed to collect any spillage, maintaining a tidy work environment and preventing floor contamination.
Acting as connectors, Splice Plates join different sections of the conveyor.
Conveyors can be built with Straight Sections and 90° Curves. Straight sections propel products forward, while 90° curves efficiently alter their direction, often onto specialized packaging equipment like labelers or accumulation tables. These curves can be used in applications with space constraints and highlight the conveyor's flexibility.
The idler end, complete with bearings and a sprocket, facilitates the smooth rotation of the chain, minimizing friction and wear.

To further reduce friction and enhance longevity, an Internal Lubrication Line delivers lubricants directly to the chain, one of the conveyor's self-maintaining capabilities.
The system's heartbeat, the Motor and Drive Shaft translates electrical energy into mechanical motion, driving the conveyor's chain and moving products along.
Advanced Conveyor Technologies
Beyond the fundamental components of conveyor systems, advanced features significantly enhance their functionality.
Variable frequency controllers adjust conveyor speed for precise operational control, while cable trays ensure the organized routing of electrical cables, important for safety considerations.
Covers protect products from external contaminants.
Laners distribute containers from single file into multiple lanes based on customer requirements. They are often placed in front of additional packaging machinery, like case packers.
More specialized additions to a conveyor, Rinse Tunnels and Blow-Off Tunnels maintain hygiene by cleaning and drying products, ensuring the integrity of the packaging remains uncompromised.
Incorporating these more advanced features into conveyor systems not only elevates the performance and adaptability of the production line but also ensures a seamless, clean, and efficient operation.
The Importance of Maintenance and Upgrades
Regular maintenance of conveyor systems is crucial for ensuring operational efficiency and preventing unplanned downtime. By addressing wear and tear through routine checks, companies can keep their conveyor lines running smoothly, extend the lifespan of the equipment, and avoid costly breakdowns. Being proactive rather than reactive with conveyor maintenance can not only prevent avoidable accidents on a production line, but makes it easier to maintain a consistent, high-quality output. Not to mention, adherence to maintenance schedules ensures compliance with industry regulations, contributing to significant long-term cost savings by reducing the need for expensive repairs or replacements.
The Future and Importance of Conveyor Systems
Conveyor systems are evolving, with innovations aimed at improving efficiency, safety, and adaptability. Alongside the original Conveyor 101 video, we hope that this introductory piece provides foundational understanding of these systems for anyone involved in the packaging industry or present on the production floor.
For those interested in exploring further, Bevco's website offers extensive resources and information on conveyor and packaging equipment. Whether you're a novice or an experienced professional, there's always something new to learn in the world of conveyor systems!
You can watch the original Conveyor 101 video here:
In Same Category
- Understanding the Essentials of Conveyor Systems
- Enhancing Efficiency with Tool-Less Quick Changeover for Your Mix Pack System
- Why Your Packaging Line Needs a Variety Pack System
- Bevco's Hand Pack Off Table: The Perfect Pack Off Solution for a Wild Goose Gosling Filler
- Thanks For Your Contribution To Flatten The Coronavirus Curve
Related by Tags
- Understanding the Essentials of Conveyor Systems
- Enhancing Efficiency with Tool-Less Quick Changeover for Your Mix Pack System
- Why Your Packaging Line Needs a Variety Pack System
- Thanks For Your Contribution To Flatten The Coronavirus Curve
- Custom Conveyor Solution: Applesauce Pouch Incline Conveyor
- Custom solutions that are tailored to suit your needs: Twist the plot with Bevco Twist Rinser
- Wet Cans or Bottles Causing Your Packaging Line Problems? Bevco’s Air Knife Tunnel Got You Covered!
- How To COPE with COVID-19 Outbreak For Breweries And Distilleries
- Bevco’s Innovative Hot-Fill Line Solution for Cap Sterilization and Cooling Challenges
- Hand Pack Off Table for Craft Brewery: Bevco’s Custom, Cost-Effective and Ergonomic Solution!
- Keep Dust out of Your Cans and Bottles
- Bevco Container and Product Stackers
- Are Worn Out Guide Rails Slowing Your Production Line?