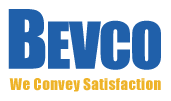
Wet Cans or Bottles Causing Your Packaging Line Problems? Bevco’s Air Knife Tunnel Got You Covered!
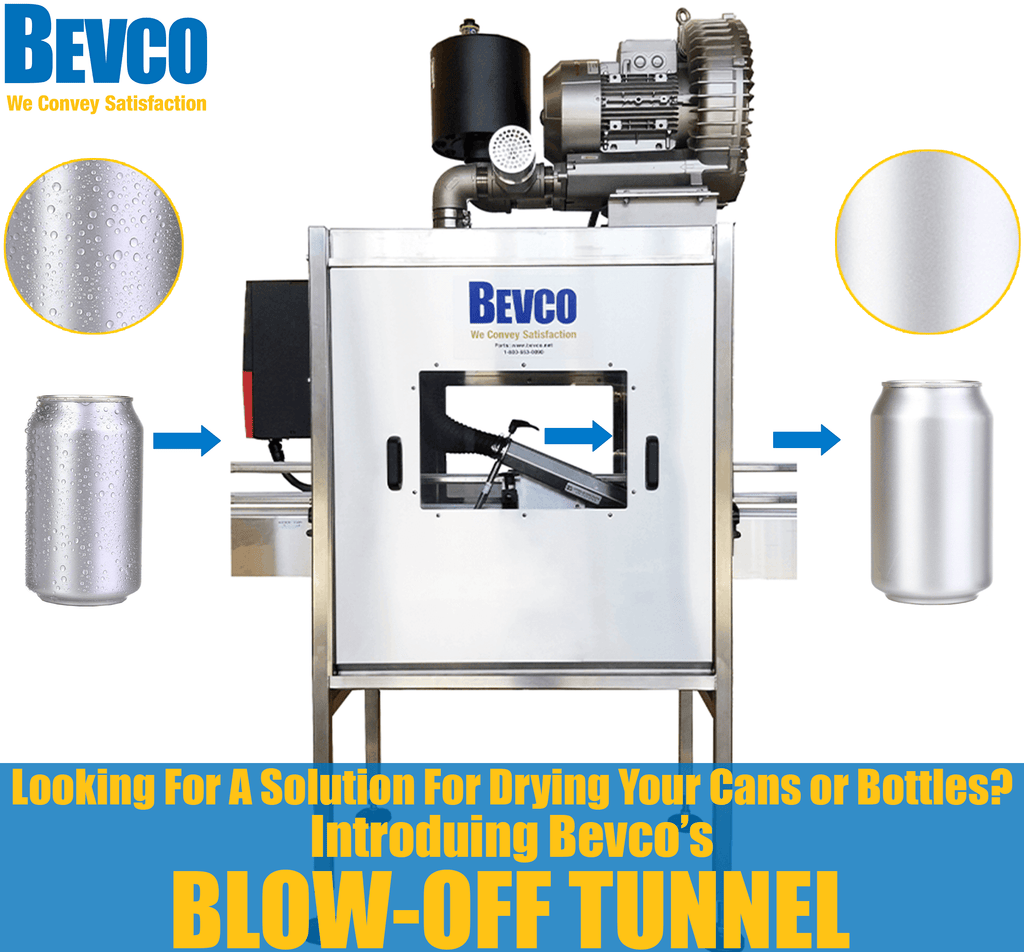
What kind of stories does the label on your product tell?
Does it contain informative content about your product such as instructions and warnings?
Does it deliver the right message to attract your target customers?
Does it represent your brand's personality and essence?
These are all very legitimate questions to ask yourself before launching your products. Labeling is one of the most powerful marketing tools as it builds brand identity. Labels help to differentiate your products from the rest on the shelves, especially in the highly competitive market of craft beer, wine, cider, pop, soda, kombucha, hard seltzer, and other beverages.
You understand the importance of labeling thoroughly, so you created a magical label design that will certainly catch your customers' attention and boost up the sales. You are excited and can't wait to launch your product. But wait a minute...why does my magical label look a bit crooked and the colors are distorted... Then you realize the damage was caused by the built-up moisture from filling and packaging. You know for sure customers nowadays will not tolerate any flaws like that on a product
You thought you figured everything out...
There’s got to be a way....
You have come to the right website!
We will walk through step by step on how our newly designed Blow-Off (Air Knife) Tunnel can solve your labeling problems and by the end of this post, you will be BLOWN away!
Application
Blow Off Tunnels (also referred to as Air Knife Tunnels, Can Dryers, Bottle Dryers, etc..) is typically used on packaging lines to blow water droplets off the exterior surfaces of cans, bottles, and other container types. They are commonly positioned at some point between the Filler and Cartoner or Case Packing machines, depending on the layout and other equipment on the line. Please refer to Item#7 in our previous blog: Canning And Bottling For Craft Brewing: Typical Can Line Layout to learn more
Also, find out how the Bevco Blow-Off Tunnel was integrated into one of our recent projects: Bevco’s Innovative Hot-Fill Line Solution For Cap Sterilization And Cooling Challenges
The main reason why moisture should be removed from container surfaces is to improve the performance of labeling and coding and to reduce the negative impact moisture can have on carton/case materials.
Learn more about Application and features
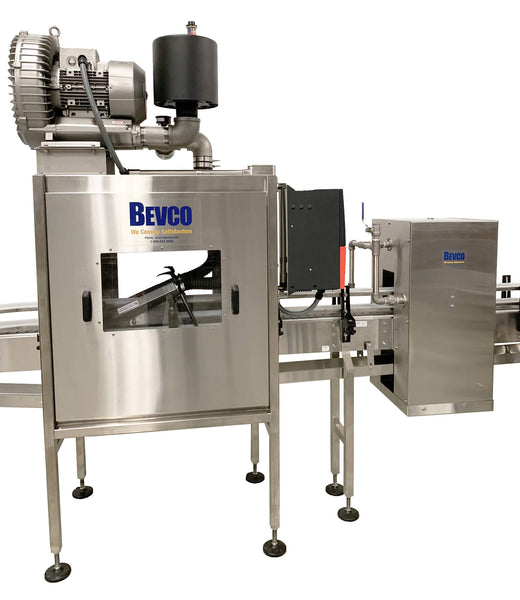
The Bevco Blow Off Tunnel is commonly used in combination with the Bevco Rinse Tunnel.
Air Knife Assembly
The Bevco Blow Off Tunnel is a stand-alone enclosure situated around a single file Conveyor that runs through the Blow-Off Tunnel. The Blow Off Tunnel can remove moisture from containers using three stainless steel Air Knives. Our standard air knife sizes are 16” side air knives and a 2” top air knife; however, sizing is customized for each application.
The first air knife is positioned above the container and blows vertically downward to remove moisture from the top of the container and to begin to force moisture down the sides of the container.
The additional two air knives are positioned on each side of the conveyor after the first air knife, and they blow air horizontally to remove moisture from the sides of the container.
Each air knife is manually adjustable in two positions vertically and horizontally using clamped rod assemblies and plastic knobs. This allows for a lot of options to fine-tune the positioning of the air knives to suit the desired application. Air knives can be adjusted very quickly without any tools by using the manually manipulated knobs. Bevco shop tests the air knife assembly prior to shipment to ensure everything is set up for your use.
Blower and Air Knife components are supplied from Republic Manufacturing
Side Panels
No change parts are needed for the Bevco Blow Off Tunnel! The two side panels are completely removable, providing access to the inside of the entire enclosure for adjustment, maintenance, and cleaning. With the side panels open, the air knives can also be easily adjusted without tools to accommodate product change over. The new design of panels has Lexan windows on each side for viewing inside the tunnels.
Floor Space
In terms of floor space, the Bevco Blow Off Tunnel is 2’-0” wide, and it is available in three lengths (3’-0” LG, 4’-0”LG, and 5’-0”LG) depending on the application; however, custom sizes can be designed on an individual basis. The height of the enclosure can vary depending on the conveyor elevation required.
In the Bevco's previous design, the blower, muffler, and motor were typically situated immediately adjacent to the Blow Off Tunnel requiring extra floor space. In Bevco’s new design, both components are mounted on top of the Blow-off tunnel frame to optimize floor space.
Water Collection and Drainage
The Blow Off Tunnel is supplied with a drain pan underneath, where excess water is collected and can be directed to the nearest drain. Bevco frequently supplies conveyors with drain pans upstream of the Blow Off Tunnel to further facilitate collection and drainage of water.
Learn more about why you need to “Keep The Production Floor Dry”
Control and Operation
There are different options available to control the Blow Off Tunnel depending on the type of control system on the rest of the packaging line.
To isolate the Blower motor, the Bevco Blow Off Tunnel is typically supplied with a disconnect switch mounted to the Blower unit. The disconnect switch is commonly controlled by a Starter or a Variable Frequency Drive (VFD) in the central Control Panel for the packaging line. When the packaging line is started and shut down, the Blower motor will turn on and off accordingly.
The disconnect switch also allows for manual shut-off of the Blower motor locally. With a Starter in the Control Panel, the blower motor will run consistently at 60 Hz with no speed adjustment; however, with a VFD in the Control Panel, the speed of the blower motor can be adjusted to suit the operator’s requirements for air pressure
For facilities where there is no central Control Panel, a local VFD with a simple controls interface can be used instead of the local disconnect switch, and the blower can be controlled by operators at the Blow Off Tunnel.
Condensation and Warming Tunnel
When condensation on the surface of cans and bottles is problematic and leads to issues with packaging materials, adding a Blow Off Tunnel alone may not be adequate. In this case, adding a can or bottle warmer can raise the temperature of the product inside the bottle or can above the dew point, reducing or eliminating the potential impact of condensation. Blow Off Tunnels are typically added to the packaging line after warming tunnels, which utilize spray water to raise the product temperature.
Click HERE for more information on Bevco Can/Bottle Warmers, refer to the link below:
Bevco’s Blow-off (Air Knife) Tunnel is a great solution to convey quality into every labeling and coding of your products. The Bevco team will work with you from start to finish. First, your existing packing line will be thoroughly assessed and then consultations will follow for seamless integration.
Please contact us at info@bevco.net or 1.800.663.0090 for more information. Let us convey satisfaction to your packing line with our 40 years of industry experience!
In Same Category
- 45 Years of Bevco: Celebrating a Legacy of Quality, Innovation, Partnership, and Community
- Understanding the Essentials of Conveyor Systems
- Enhancing Efficiency with Tool-Less Quick Changeover for Your Mix Pack System
- Why Your Packaging Line Needs a Variety Pack System
- Bevco's Hand Pack Off Table: The Perfect Pack Off Solution for a Wild Goose Gosling Filler
Related by Tags
- Understanding the Essentials of Conveyor Systems
- Enhancing Efficiency with Tool-Less Quick Changeover for Your Mix Pack System
- Why Your Packaging Line Needs a Variety Pack System
- Thanks For Your Contribution To Flatten The Coronavirus Curve
- Custom solutions that are tailored to suit your needs: Twist the plot with Bevco Twist Rinser
- Wet Cans or Bottles Causing Your Packaging Line Problems? Bevco’s Air Knife Tunnel Got You Covered!
- How To COPE with COVID-19 Outbreak For Breweries And Distilleries
- Bevco’s Innovative Hot-Fill Line Solution for Cap Sterilization and Cooling Challenges
- Hand Pack Off Table for Craft Brewery: Bevco’s Custom, Cost-Effective and Ergonomic Solution!
- Bevco's Custom Fabrication
- Keep Dust out of Your Cans and Bottles
- The Bevco Cooling Tunnel: A Cool Solution for a Hot-Filled Product
- Bevco Container and Product Stackers
- Modular Conveyors Provide Adapabilty in the Bottling Line
- BEVCO: Continuing to Modernize and Automate our Manufacturing Process to Ensure our Competitive Edge.
- Are Worn Out Guide Rails Slowing Your Production Line?