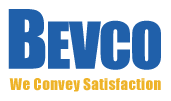
Canning and Bottling for Craft Brewing: Variety Packs
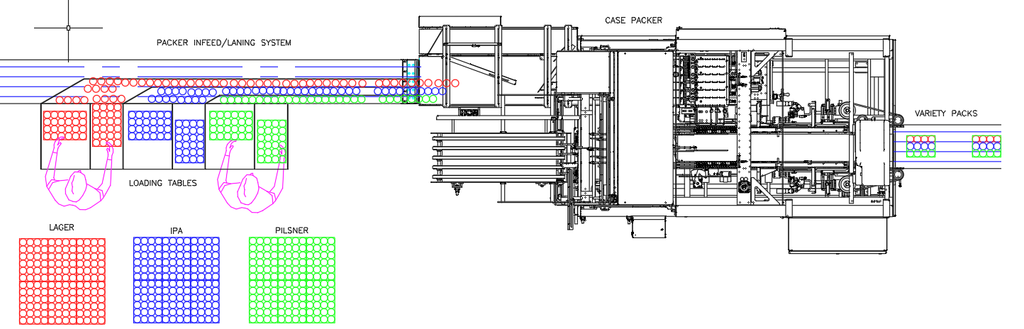
They say variety is the spice of life. It has also been said that beer is the spice of life. Its no surprise then, that variety packs of craft beer are flying off the shelves of liquor stores everywhere. But packaging variety packs can be a challenge for brewing operations.
Most breweries have only one packaging line, so the option of filling multiple different types of beers simultaneously and merging the production lines into a single case packer with a lane for each beer type is just a dream.
In reality, packaging for variety packs demands more time and labour than packaging a single type of beer but an efficient method can be made possible with a few equipment additions prior to the case packer: unloading tables and a lane system.
Hand Packing:
The first and most simple option for packaging variety packs is doing it all by hand. This option is slow and labour intensive but requires no additional equipment for the existing packaging line. This type of packaging is recommended for small scale brewing.
To demonstrate this, let’s imagine Example Brewery wants to package 300 variety packs (12 beers per box); 4 Lagers, 4 IPAs and 4 Pilsners per case. This means they will need 1200 of each beer. They currently have a filler/capper and load all their beers onto 24 beer flats by hand. First the brewery will need to do a production run for each type of beer and stack the flats on pallets. The brewers have calculated they need 50 flats of each beer (50*24=1200). The brewers will bring a pallet of each beer type into a common area (usually around a table) and take 4 beers from the Lager pallet and place them in the variety pack box, 4 beers from the IPA pallet and place them in the box, and 4 beers from the Wheat Ale Pallet and place them in the box. Once the 12 beers have been loaded into the variety pack, it is sealed and placed on a new pallet, ready for distribution.
This method is labour intensive because 1 – 3 workers are needed to fill the variety packs by hand. It is time consuming as well.
Unloading Stations and Packer Infeed Lanes:
The process of packaging variety packs for most breweries involves unloading beer cases by hand into a series of lanes that feed the case packer. To do this, hand packing tables need to be incorporated in the production line in front of the case packer as well a as removable/adjustable laning system to feed each lane of the packer. Lots of room beside these hand packing tables is recommended so pallets of beer can be more easily maneuvered into place where necessary.
Sales of beer have been going well and Example Brewery have decided to invest in a higher speed filler and automatic case packing system. This case packer can fill 24 cases and 12 cases of beer. When filling cases with one type of beer, the packaging machine takes a bulk infeed of cans and separates them into lanes then drops them into the case.
Example Brewery kept filling the variety packs by hand after investing in the new equipment, but decided that this way of packaging was too inefficient and costly in labour hours so they started to explore other options.
The solution was to modify the infeed of the case packer so it could be used to fill the variety pack boxes. Example Brewing invested in a new adjustable/removable set of lanes and a hand packing table for loading cans onto the production conveyor.
When packaging variety packs, workers first need to lower the lanes into place and move a pallet of Lager, pallet of IPA, and pallet of Pilsner next to the hand loading stations. Next, workers load Lagers by hand from the pallet onto the loading table and push the beers into the Lager lane. The same goes for the IPA and Pilsner. The case packer will then drop 4 cans of each beer type from its lane into the box and seal it, resulting in a quick and efficient way to package the variety packs.
This method is better suited for medium scale brewing. Workers still need to unload beers of each type from pallets into their individual lanes, but the cases are packed automatically by the case packer which is much more efficient than the hand packing option.
Loading Stations:
There are some options and different configurations of loading stations that are available. Beers are always unloaded from a pallet onto a stainless steel table but from the steel table to the conveyor system there are some options.
Some breweries will choose to directly load the cans from the stainless table onto the packer infeed conveyor. Other breweries who desire more accumulation in front of their case packer can unload onto a bi-directional accumulation table. This will allow more cans to be placed into the lanes, resulting in less stoppage time of the case packer. When the brewery is not running variety packs, the lanes lift up and the bi-di table will provide accumulation for the infeed of the packer.
In Same Category
- 45 Years of Bevco: Celebrating a Legacy of Quality, Innovation, Partnership, and Community
- Understanding the Essentials of Conveyor Systems
- Enhancing Efficiency with Tool-Less Quick Changeover for Your Mix Pack System
- Why Your Packaging Line Needs a Variety Pack System
- Bevco's Hand Pack Off Table: The Perfect Pack Off Solution for a Wild Goose Gosling Filler
Related by Tags
- Enhancing Efficiency with Tool-Less Quick Changeover for Your Mix Pack System
- Why Your Packaging Line Needs a Variety Pack System
- Thanks For Your Contribution To Flatten The Coronavirus Curve
- Custom solutions that are tailored to suit your needs: Twist the plot with Bevco Twist Rinser
- How To COPE with COVID-19 Outbreak For Breweries And Distilleries
- Bevco’s Innovative Hot-Fill Line Solution for Cap Sterilization and Cooling Challenges
- Hand Pack Off Table for Craft Brewery: Bevco’s Custom, Cost-Effective and Ergonomic Solution!
- Canning and Bottling for Craft Brewing: Variety Packs
- Are Worn Out Guide Rails Slowing Your Production Line?
- Keep the Filler Going!