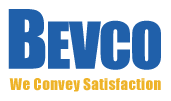
Custom solutions that are tailored to suit your needs: Twist the plot with Bevco Twist Rinser
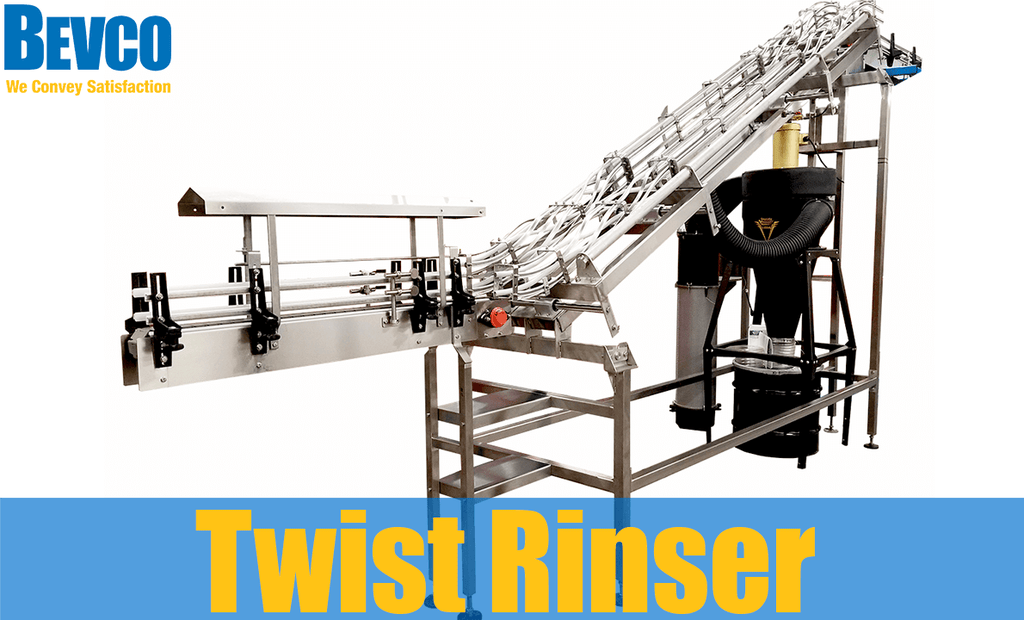
There is a reason why every man should own a tailored suit. Because it is customized to your satisfaction, you can be assured there is quality in every detail down to the last seam.
Similarly, every brewery should get their packaging line "tailored to suit" its needs to optimize production efficiency. This is what Bevco does best. For the last forty years, our reputable industry-leading technical specialties in the beverage and food industry have resulted in complete satisfaction for every client.
Check out some of custom solutions we have offered to our clients recently:
- “Hot-Filled Line Solution” for a beverage manufacturer with limited space
- “Ergonomic Hand Pack-Off Solution” for a craft brewery
To keep up with growing needs for custom solutions, we recently added a new addition to our rinser family:
The Twist Rinser
The primary function of the Bevco Twist Rinser is to blow particles out of empty cans prior to filling.
The Twist Rinser first turns the empty cans upside down.
The cans then flow over a series of ionized air nozzles which blow particulates out of the cans.
The containers then proceed into the lower portion of the Twist Rinser where they are turned back upright and sent on to the filler infeed conveyor.
When Twist Rinser is running different product sizes (in this case 12oz & 16oz cans) two sizes of helical guiderail “twisters” are needed as the guiderails must surround the container as it passes through the unit.
This requires a carriage mechanism to allow for quick changeover flow from one size of guiderail / laneway to the other. Ease of changeover was fundamental in the design of the Bevco Twist Rinser so the changeovers can be easily repeated with little to no adjustments needed.
Welcome to the Tailor Shop for the Beverage Manufacturers
In one of our recent projects, we were approached by a client who had issues with their current non-Bevco Twist Rinser and areas where their equipment could be improved.
- Their Twist Rinser was bolted together instead of welded, so the components of the rinser would loosen over time due to vibration and temperature change. Whenever operators attempted to tweak any loose or misaligned guiderails, the misalignment actually became more pronounced, causing the products flowing through the unit to jam and halt production.
- When they switched between 12oz and 16oz containers, operators would have to “disassemble” the upper infeed dead plate and reassemble it once the change-over had been completed. They would then need to tweak the guiderails, so their alignment would not cause the containers to jam. This caused significant amount of time and effort.
After identifying their issues, Bevco came up with custom solutions to overcome their challenges.
Custom Solution #1
We incorporated minimal fasteners on the Twist Rinser and welded the components together as much as possible, thus removing any potential for the equipment to become misaligned or requiring adjustment.
Custom Solution #2
Bevco’s design solution was to create a “dynamic dead plate” which requires no disassembly. This component remains fully attached to both Twist Rinser laneways and the upper infeed conveyor.
All that is required to changeover from 12oz to 16oz product flow is to unlock the 2 hard stops and push the guiderail carriages to the new position and then relock the hard stops.
Changeover takes about 10 seconds and there is no misalignment as the hard stops create a repeatable guiderail / laneway alignment; ensuring the containers do not jam in the unit and stop production.
Just like how suits need to be tailored according to every man’s unique body types, every brewery needs its own solution to optimize production efficiency. Over the last forty years, we have dealt with hundreds of different clients and their unique challenges. Bevco’s exclusive custom solution will convey customized satisfaction to you and your packaging line!
In Same Category
- 45 Years of Bevco: Celebrating a Legacy of Quality, Innovation, Partnership, and Community
- Understanding the Essentials of Conveyor Systems
- Enhancing Efficiency with Tool-Less Quick Changeover for Your Mix Pack System
- Why Your Packaging Line Needs a Variety Pack System
- Bevco's Hand Pack Off Table: The Perfect Pack Off Solution for a Wild Goose Gosling Filler
Related by Tags
- Understanding the Essentials of Conveyor Systems
- Enhancing Efficiency with Tool-Less Quick Changeover for Your Mix Pack System
- Why Your Packaging Line Needs a Variety Pack System
- Thanks For Your Contribution To Flatten The Coronavirus Curve
- Custom solutions that are tailored to suit your needs: Twist the plot with Bevco Twist Rinser
- Wet Cans or Bottles Causing Your Packaging Line Problems? Bevco’s Air Knife Tunnel Got You Covered!
- How To COPE with COVID-19 Outbreak For Breweries And Distilleries
- Bevco’s Innovative Hot-Fill Line Solution for Cap Sterilization and Cooling Challenges
- Hand Pack Off Table for Craft Brewery: Bevco’s Custom, Cost-Effective and Ergonomic Solution!
- Canning and Bottling for Craft Brewing: Variety Packs
- Keep Dust out of Your Cans and Bottles
- Are Worn Out Guide Rails Slowing Your Production Line?